Category: Uncategorized
PNK Group Announces Acquisition of Industrial Site in Southern New Jersey
PNK Group Announces Acquisition of Industrial Site in Southern New Jersey.
Industrial developer PNK Group has finalized the acquisition of a land parcel in June 2025 in the city of Waterford, Camden County, Southern New Jersey. The site, named PNK Waterford, spans over 53 acres and marks another step in the company’s growing presence in the state. PNK Group plans to construct an industrial facility of approximately 270,000 square feet on the site, further strengthening the region’s logistics and industrial infrastructure.
PNK buildings are known for their versatility, supporting a wide range of uses—from manufacturing to storage and distribution. Due to the increased material density of their structures, PNK Group facilities offer enhanced durability, making them well-suited for production needs.
Southern New Jersey continues to be in high demand among industrial tenants, thanks to its strategic location, proximity to four major seaports, high population density, and access to a skilled labor force. The site is located at the intersection of Routes 30 and 73, two key transportation arteries providing fast access to I-295 and the New Jersey Turnpike. Within a 150-mile radius, the area reaches a population of approximately 35 million people, including the metropolitan areas of New York, Philadelphia, Baltimore, and Washington, D.C.
The project is part of a 20-year PILOT (Payment In Lieu Of Taxes) program, offering substantial tax incentives for future tenants and users. A redevelopment agreement for the site has been signed with Waterford Township.
For construction, PNK Group utilizes its proprietary Building Assembly Set (BAS) system. One of the key advantages of this method is its simplicity. BAS elements are designed for easy assembly, significantly simplifying the construction process. By using standardized large-format blocks pre-manufactured at the company’s own factories in Georgia and Pennsylvania, PNK
Group is able to build faster than the market average.
PNK Group continues to accelerate its land acquisition efforts along the East Coast, having recently closed additional deals in Connecticut, Pennsylvania, Virginia, and Georgia.
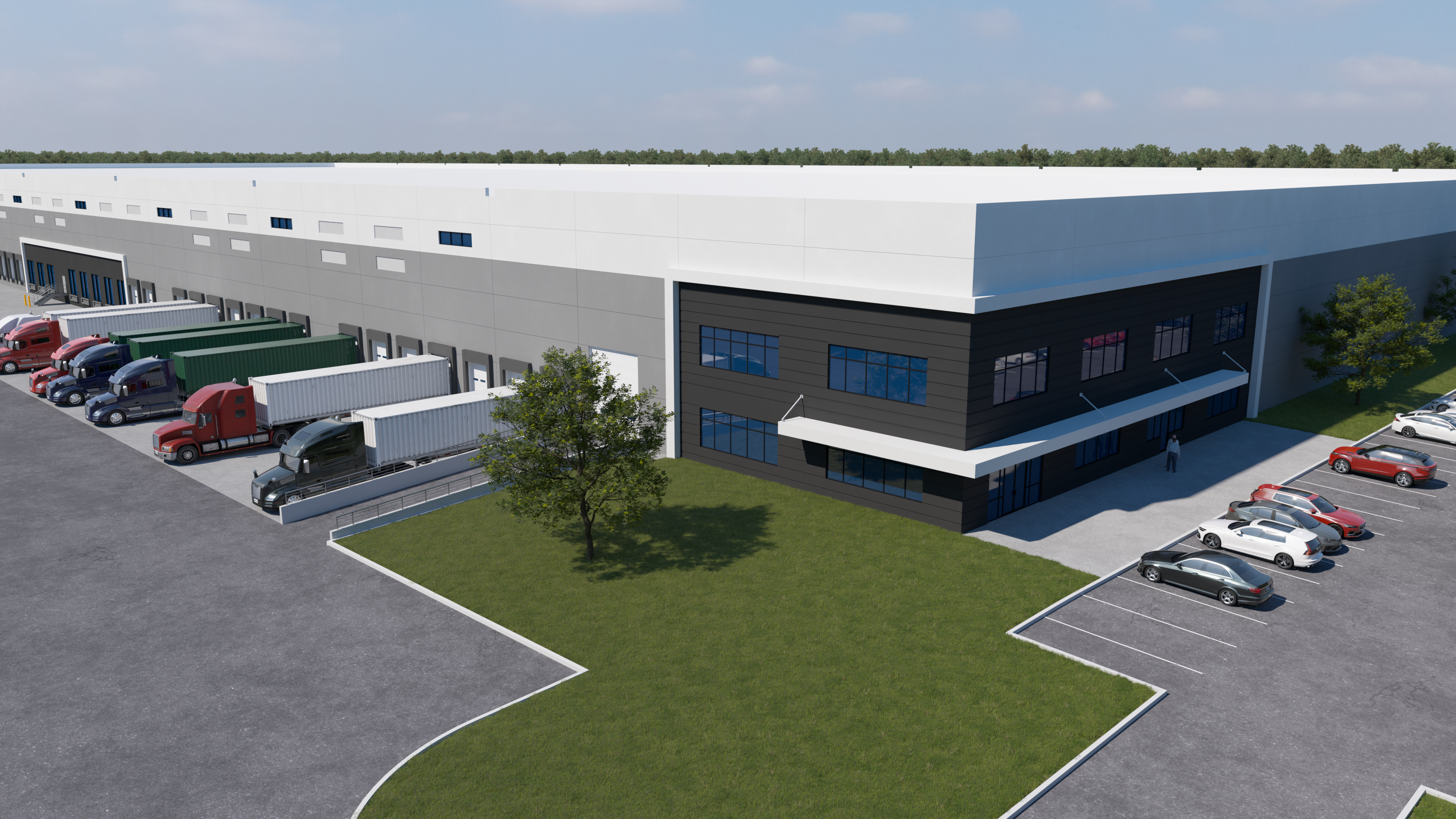
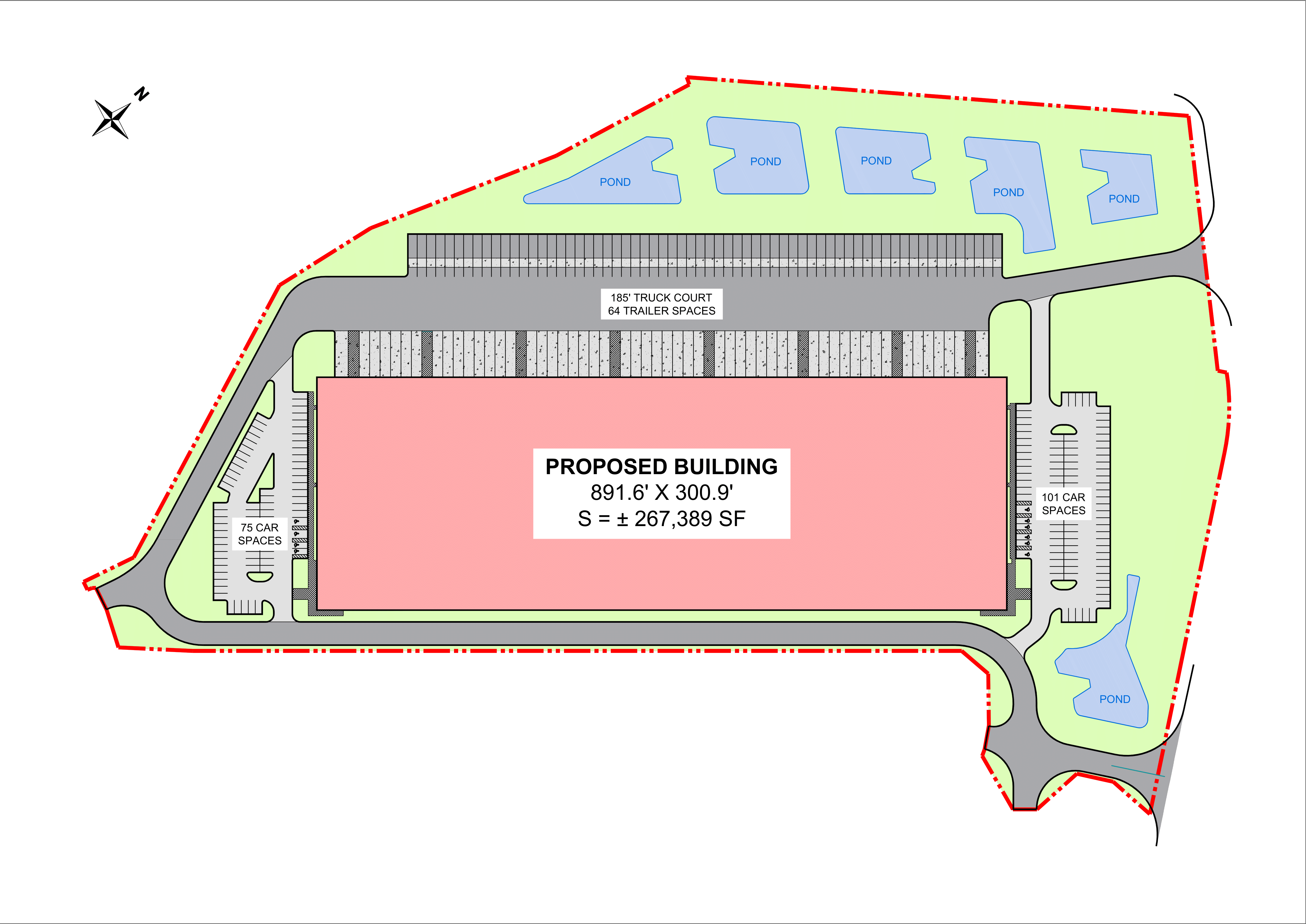
PNK Group Breaks Ground on New Facility in Virginia
Industrial developer PNK Group will construct an 846,000-square-foot facility in the Greater Richmond area.
On April 17, PNK Group held a groundbreaking ceremony for its new development, PNK Ashton Park, located in Chesterfield County, Virginia. The new multi-functional facility will span 846,000 square feet on a site covering 86.6 acres. It is designed for flexible use by either a single tenant or multiple occupants.
According to PNK Group Partner Mark Stiles, the region holds strategic importance for the company, while the project itself is of great interest to local authorities. This is reflected in the participation of Chesterfield County leadership and the Chesterfield Economic Development Office at the event.
“The Greater Richmond region is among the top five markets in the Southeast U.S. with the lowest vacancy in Class A industrial space,” said Jim Ingle, Chair of the Chesterfield County Board of Supervisors and Bermuda District Supervisor. “I understand from our economic development team that there have been several visits by prospects to the site, so I know the building will be leased in no time.”
The region’s strong position within the state is further reinforced by the presence of major national tenants such as FedEx, Lego, Sabra, and Church & Dwight, along with prominent local companies like Shepherd Electric and A&A Transfer. Demand continues to grow, while available land for new development remains limited.
PNK Group employs proprietary construction technology that significantly streamlines the building process compared to traditional methods. Utilizing standardized large-block components produced at the company’s manufacturing facilities in Georgia and Pennsylvania, PNK can deliver buildings faster and more efficiently than market averages. This modular method also reduces the need for a large onsite workforce and heavy equipment.
PNK Group’s facilities are highly versatile and suitable for a variety of uses — from manufacturing to storage and distribution. With ceiling heights of up to 45 feet and reinforced concrete structures, the buildings are engineered to support heavy equipment and cranes with capacities of up to 8 tons, enabling tenants to operate across a broad range of industrial applications.
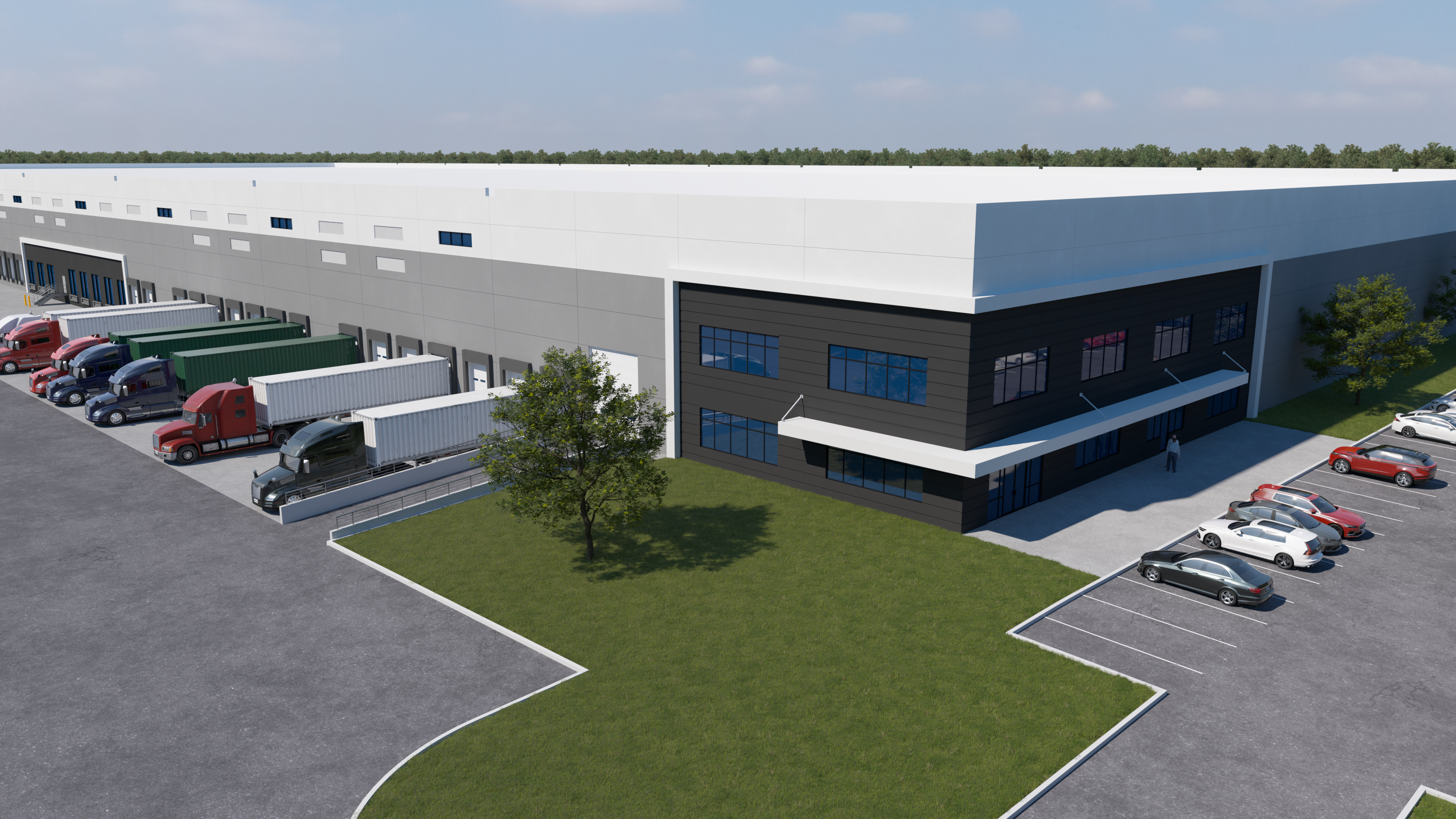
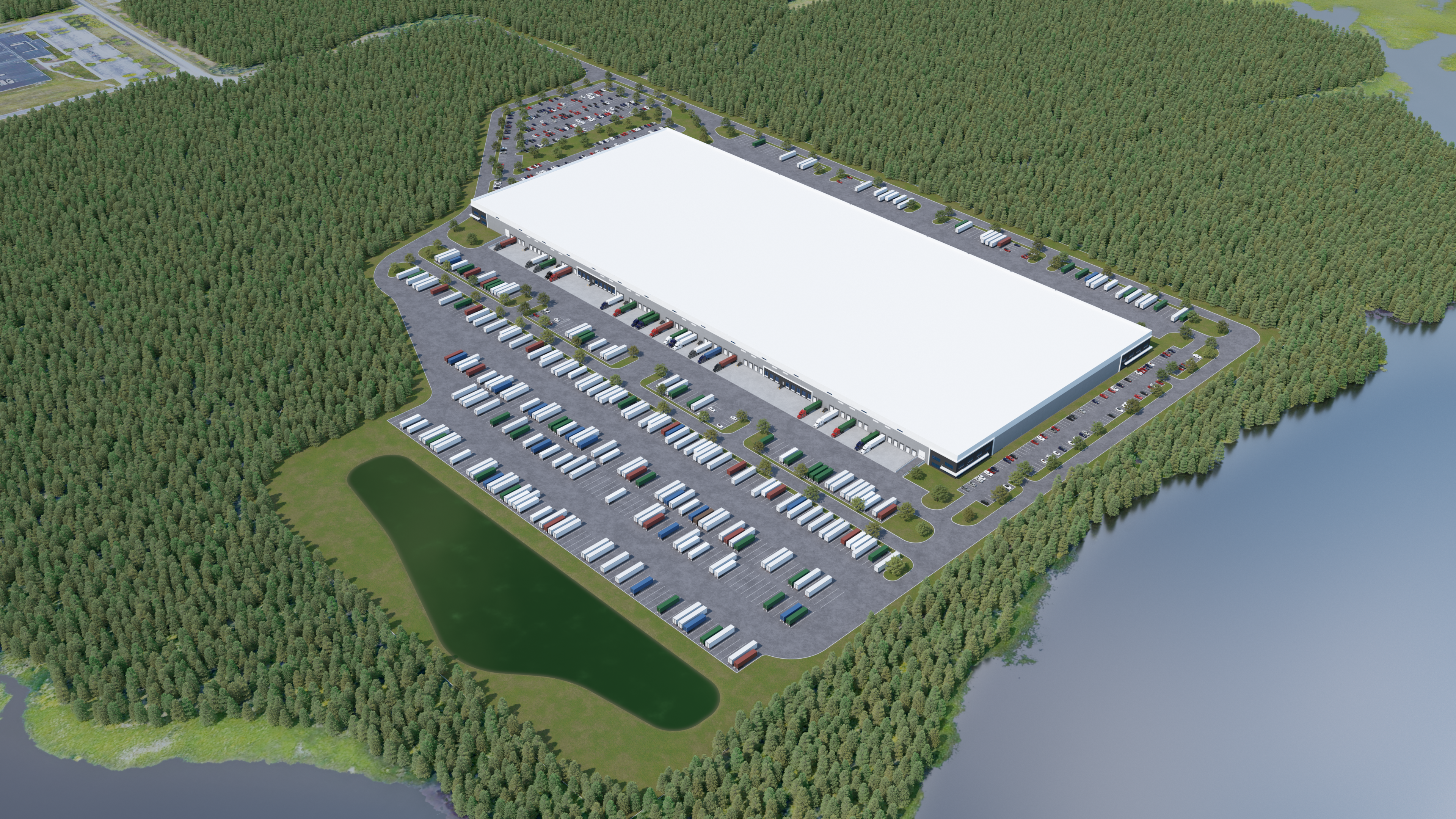
Innovative Technologies at Every Stage of the Construction Process
The PNK Group Approach: Modular and Factory-Produced Components
One of the defining features of our construction process is the use of factory-made elements that are ready for assembly, much like a construction kit. These preassembled elements are produced and stored in advance at our own facilities, meaning they’re ready to be transported to the site once construction begins. By utilizing modular construction techniques, we eliminate the need for complicated and technically complex operations during assembly, reducing the overall construction timeline. In essence, we’ve simplified the assembly process, significantly speeding up delivery times while ensuring that quality and structural integrity are maintained. This approach not only saves time but also reduces the human factor—minimizing errors and improving overall construction quality. The use of standardized, pre-made components ensures consistency across projects, resulting in stronger, more durable buildings that meet the needs of even the most demanding industries, from manufacturing to logistics. Contact us if you are interested in learning more about our innovative approach.Why PNK Group’s Modular Construction is a Game Changer
Our Building Assembly Set (BAS) system is at the heart of this innovation. This approach allows us to pre-assemble building elements at our factory, reducing the complexity of on-site construction. Once the pre-made components arrive at the construction site, the process becomes much simpler and faster, minimizing the need for skilled labor and reducing the time spent on-site. Because these building components are produced in a controlled factory environment, we also see increased material efficiency, which leads to fewer material waste and reduced environmental impact. This, in turn, results in cost savings that we pass on to our clients. The outcome is a stronger structure, built with higher-quality materials—ideal for manufacturing environments, storage, or logistics centers.Main Stages of the Construction Process
At PNK Group, we follow a systematic construction process that integrates cutting-edge technologies to create a seamless and efficient workflow. Here are the main stages of our construction process:1. Manufacturing and Preassembly of Building Components
After the site is secured, we begin the manufacturing and preassembly phase. This is where our factory-made Building Assembly Sets (BAS) come into play. Each element of the building, including the foundation, walls, columns, roof systems, and floors, is pre-manufactured in our own state-of-the-art facilities in Pennsylvania and Georgia. This controlled environment allows us to optimize quality, minimize waste, and significantly reduce on-site assembly time. These pre-manufactured elements are stored and ready to be shipped to the site as soon as is ready to begin.2. Transportation and On-Site Assembly
One key benefit of working with PNK Group is that our standard components are manufactured constantly, making it possible to begin construction immediately. This is where the true advantage of our modular approach becomes clear. On-site assembly is streamlined and simplified, as most of the work has already been completed in the factory. The preassembled elements are quickly and efficiently put together, with minimal labor and machinery required on-site. Because the components are standardized and pre-engineered, the assembly process is fast and precise, minimizing errors and reducing the need for specialized on-site labor.3. No Wet Cycles – A Key PNK Group Distinction
A standout feature of PNK Group’s construction process is our absence of wet cycles. Traditional construction often involves processes that rely on wet materials, like concrete pouring or bricklaying, which can be affected by weather conditions and require longer curing times. These wet cycles can lead to delays and environmental emissions, such as water runoff and excess moisture. At PNK Group, we’ve eliminated wet cycles in our process, reducing the potential for delays due to weather and minimizing the environmental impact of construction. This ensures a faster build time and a cleaner, more sustainable construction process, aligning with our commitment to reducing emissions and building sustainably.4. Final Touches and Quality Assurance
Once the structure is assembled, we move on to the finishing touches, which may include the installation of utilities, HVAC systems, flooring, and any specialized equipment or technology needed by the client. Our quality assurance process ensures that each building meets our high standards for safety, structural integrity, and performance. Before the building is handed over, a final inspection is conducted to ensure that everything is in perfect working order and ready for immediate use.Technology’s Role in Reducing Construction Times
By embracing factory manufacturing and modular construction techniques, PNK Group has revolutionized the speed and efficiency of industrial development. Our BAS system and modular approach allow us to build 2-3 times faster than traditional construction methods. This enables us to complete projects on time while maintaining the highest quality standards.Why Choose PNK Group’s Innovative Construction Process?
- Speed: Our modular construction and BAS system reduce assembly times by 2-3 times compared to traditional methods.
- Efficiency: With pre-manufactured elements and an absence of wet cycles, we minimize waste and environmental impact.
- Quality: Our factory-controlled manufacturing ensures the highest quality materials and precision in assembly.
- Adaptability: Our buildings are highly flexible, capable of supporting a variety of industries and operations.
A Full Spectrum of Turnkey Solutions Across the U.S.
At PNK Group, we understand that delivering high-quality industrial real estate goes beyond just building structures—it’s about offering comprehensive solutions that help our clients achieve their business goals. From project financing to turnkey development, we provide a full range of services to ensure every aspect of your industrial development needs is covered.
With over 15 million square feet of industrial projects under development across the United States, our team is focused on providing complete, flexible, and cost-effective services. Whether you are looking for a custom-built facility or a high-performance warehouse, PNK Group is your trusted partner from start to finish.
Our Full Range of Turnkey Development Services
At PNK Group, we pride ourselves on our ability to manage the entire development process, offering everything from initial planning to the completion of fully operational buildings. Here’s an overview of the services we offer:
1. Comprehensive Project Financing
We understand that securing financing for a large-scale industrial project can be a daunting task. That’s why PNK Group provides project financing where necessary, partnering with clients to make sure they have the financial resources required to move forward with their projects.
With a fixed-price contract model, we help clients plan and budget effectively, ensuring no surprises during the construction process. We take the complexity out of financing, allowing you to focus on your business while we handle the details. This makes the entire process more predictable and reduces financial risk for our clients.
2. Full-Service Design and Engineering
Our services go beyond just building structures. We offer design and engineering solutions tailored to your specific needs, ensuring that every building we develop is optimally suited to your operations. Our expert team works with you to plan, design, and engineer buildings that support your exact requirements, from layout to building configuration.
We understand that every business is different, and we use our expertise to deliver functional, adaptable spaces that support your long-term growth. Whether it’s incorporating specialized equipment or adjusting the layout for workflow efficiency.
3. Turnkey Construction and Project Management
From start to finish, we handle every aspect of the construction process. Our turnkey construction services ensure that your project is completed on time and within budget, without the hassle of coordinating with multiple contractors. With PNK Group, you have a partner for all phases of development, streamlining communication and ensuring a smoother construction process.
Our project management team oversees everything from procurement and permits to site preparation and final inspection, ensuring that your project runs seamlessly. Our experience and attention to detail allow us to deliver high-quality industrial buildings quickly and efficiently.
4. Customizable and Flexible Building Solutions
One of the core values of PNK Group is flexibility. We understand that your business needs may evolve over time, and our buildings are designed with that in mind. We offer customizable solutions that can be adjusted to meet changing needs, whether that’s installing heavy machinery or upgrading for additional storage space.
From large distribution centers to manufacturing facilities, PNK buildings are engineered to accommodate a wide variety of functions, making them perfect for businesses in logistics, manufacturing, and beyond.
5. Site Acquisition and Development
Looking to expand your operations? PNK Group offers site acquisition services, identifying prime land locations to support your growing business. With a keen eye for high-potential land, we focus on securing sites in regions that are strategically located for ease of access to transportation networks, markets, and supply chains.
We are actively exploring opportunities in high-demand land markets, particularly in key East Coast and Central states. Our site acquisition expertise allows us to find land in the most promising regions and navigate the complexities of zoning, environmental regulations, and permitting.
Our Projects: Where Are We Making an Impact?
PNK Group has made a significant impact in industrial development across the United States, with ongoing and completed projects totaling over 15 million square feet. We currently have a strong presence in regions that are seeing major growth in industrial and commercial real estate, and we are expanding our footprint across the country.
Our past and current projects include developments in the following states:
- New York
- New Jersey
- Pennsylvania
- Connecticut
- Georgia
- Virginia
- Texas
- North Carolina
As part of our continued growth strategy, PNK Group is actively expanding on the East Coast and Central U.S. regions, with plans to extend our network across the country. We are constantly exploring new opportunities in Florida, South Carolina, and other states where industrial demand is on the rise. Check out our current available properties.
Exploring Opportunities for Land Acquisition
In addition to our ongoing developments, PNK Group is actively seeking out land opportunities in some of the country’s most promising regions. We are focused on securing strategic land sites that can support the growing demand for industrial space in markets such as:
- Florida
- South Carolina
- North Carolina
- New York
- New Jersey
- Pennsylvania
- Connecticut
- Georgia
- Virginia
- Texas
As the industrial real estate landscape continues to evolve, PNK Group remains dedicated to finding locations that meet the growing needs of businesses and help clients stay ahead of the curve in an ever-competitive market. Contact us today if you are interested in learning more about land acquisition opportunities.
Why Choose PNK Group?
At PNK Group, we are more than just a construction company. We are a full-service partner that takes your industrial development project from concept to completion.
We are proud of our ability to offer a comprehensive, one-stop solution for industrial development, ensuring your projects are completed efficiently, cost-effectively, and to the highest standards.
Versatility & Customization: Tailoring Industrial Buildings to Meet Unique Needs
At PNK Group, we understand that no two industries are the same—and neither are their building requirements. From logistics to manufacturing, from high-tech to warehousing, our industrial buildings are engineered to be incredibly versatile, making them suitable for a wide range of applications across multiple sectors.
Our unique approach allows us to adapt and customize solutions based on the specific needs of each client. Whether it’s heavy-duty operations requiring robust load-bearing capacity or a facility that needs precise climate control, we offer functional, scalable, and flexible solutions that help businesses thrive in today’s competitive environment.
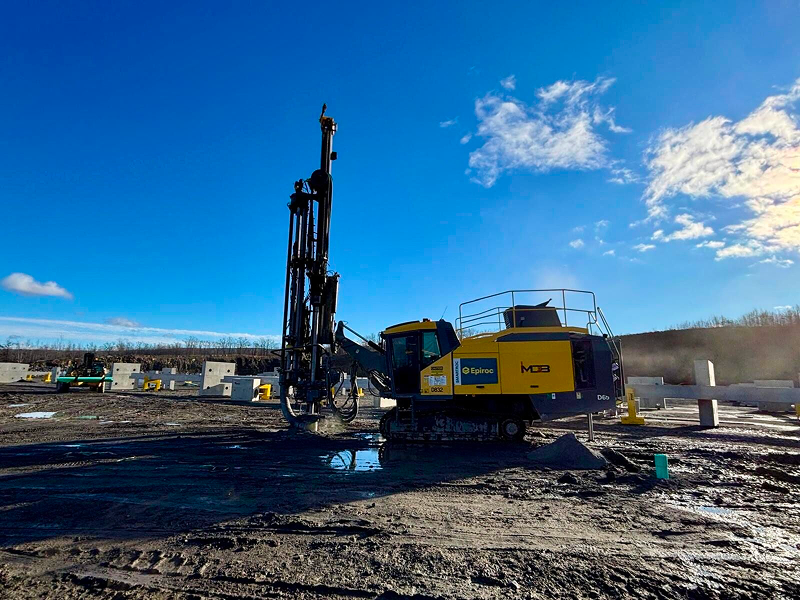
Serving a Wide Range of Industries
PNK Group’s industrial buildings are not limited to just one type of business. We work with a diverse range of industries, providing tailored solutions that meet the unique demands of each. Here’s a closer look at how we adapt our buildings to the needs of various sectors:
1. Logistics and Distribution
In the fast-paced logistics and distribution industry, speed and efficiency are paramount. Our buildings offer high ceilings (up to 40 feet clear height) and large, flexible floor plans, making them perfect for handling goods at scale. With wide loading docks and insulated doors designed to withstand the wear and tear of daily operations, our facilities support the heavy movement of freight with ease.
For example, the 40,000 lbs. lifting capacity in our prefab precast dock pits allows for heavy trucks and containers to be efficiently loaded and unloaded. Modular design features like adjustable staging bays (60’ to 75’ deep, depending on the building size) further enhance the adaptability of these spaces to meet the evolving needs of logistics businesses.
2. Manufacturing
For manufacturers, flexibility is key. PNK Group’s industrial buildings are engineered to support a wide range of production processes, from light assembly to heavy-duty manufacturing. Our buildings are designed with reinforced concrete columns that can support overhead cranes of up to 8 tons—ideal for facilities where large equipment, machinery, or assembly lines are required.
Additionally, our buildings come with high load-bearing capacity floors (8-inch slab on grade, reinforced with steel mesh and vapor barrier), which make them perfect for housing the heavy machinery typical in manufacturing operations. These features, combined with our ability to tailor space configurations, ensure that each manufacturing space we build can evolve with the growing demands of the business.
3. Warehousing & Storage
With the increasing demand for efficient warehousing solutions, our buildings provide ample storage capacity with features like insulated dock doors and robust foundations for the heaviest loads. The TPO 80 mil roof system with R-25 insulation ensures the building remains energy-efficient, reducing long-term operational costs, while the prefabricated 3-layered precast concrete walls protect against the elements, ensuring your goods are stored safely.
Our standard configuration also includes motion sensor lighting (30FC on 15-foot pendants), optimizing energy use while ensuring warehouses are well-lit, functional, and secure around the clock.
Tailoring Buildings to Specific Client Needs
At PNK Group, we pride ourselves on offering customizable solutions to meet the unique demands of each client. While we provide standard configurations to ensure efficiency and cost-effectiveness, we also understand that every business has its own specific needs. That’s why our industrial buildings can be adapted in several ways, including:
- Load-bearing capacity adjustments for heavier equipment or specialized machinery
- Crane installation for industries requiring overhead lifting systems (up to 8 tons)
- Internal and external finishes tailored to the client’s specifications (e.g., exterior paint colors, internal finishes, and specialized windows)
- HVAC and air change systems tailored to the client’s operational requirements, ensuring optimal climate control
Why Choose PNK Group?
What sets PNK Group apart is our ability to deliver multifunctional industrial buildings that not only meet but exceed the expectations of businesses across diverse sectors.
Whether you’re in logistics, manufacturing, or warehousing, PNK Group has the expertise and the technology to build the perfect space for your business. Contact us today if you are interested in learning more about current opportunities.
Unique Solutions to Common Industrial Problems: How PNK Can Help
In the fast-paced world of industrial construction, time is money. Developers are looking for faster project delivery, cost-effective solutions, and flexible buildings that can adapt to changing demands. As the industrial sector grows, traditional construction methods often fall short in meeting these challenges. At PNK Group, we’re tackling these problems head-on, transforming how industrial buildings are built to deliver faster, smarter, and more versatile solutions.
The Problem: Slow, Inflexible, and Costly Traditional Construction
Conventional construction techniques come with significant challenges that can delay projects, increase costs, and reduce flexibility. Builders often rely on a complex web of supply chains, subcontractors, and labor-intensive methods that result in longer construction times and unpredictable project outcomes.
For companies that need to get their facilities up and running quickly, this can mean lost revenue, stalled operations, and increased financial risk. What’s more, as industries evolve, the demand for buildings that can be easily repurposed for various functions—whether for manufacturing, warehousing, or logistics—has never been greater. Traditional construction often doesn’t provide the flexibility required to meet these changing needs without substantial renovation costs.
PNK’s Solution: Speed, Versatility, and Architectural Flexibility
At PNK Group, we’ve redefined the way industrial buildings are constructed, addressing these key pain points with our innovative approach. Here’s how we do it:
1. Fast Construction with Building Assembly Sets (BAS)
One of the most significant advantages we offer is the speed of construction. Thanks to our independent supply chain and the production of Building Assembly Sets (BAS) at our own state-of-the-art plants in Pennsylvania and Georgia, we eliminate the common delays caused by third-party suppliers and labor shortages. This self-reliance not only ensures that materials are readily available when needed, but it also allows us to control quality and timelines effectively.
Our modular approach to construction utilizes preassembled elements—similar to a giant building “constructor set”—which are stored in stock and transported directly to the site. Once at the construction location, these elements can be rapidly assembled, significantly speeding up the build process.
The result? We complete industrial buildings 2 to 3 times faster than the overall market average, allowing businesses to start operations much sooner. This reduction in construction time helps clients realize their return on investment more quickly, while also minimizing the disruptions that can come from long construction timelines.
2. Universal Use Across Industries
PNK Group’s industrial buildings are designed with versatility in mind. Whether you need a manufacturing facility, a warehousing space, or a distribution center, our buildings can be adapted to meet your specific requirements. With clear building heights of up to 40 feet and ceiling heights reaching 45 feet, our structures can accommodate large-scale operations, including the storage of hazardous materials and the installation of heavy equipment like overhead cranes.
Moreover, our reinforced concrete frame systems provide outstanding load-bearing capacity, making it possible to incorporate a wide range of manufacturing technologies and logistics systems. This flexibility ensures that the building can easily transition from one function to another—whether it’s shifting from a warehouse to a manufacturing facility or expanding capacity to accommodate new production lines—without the need for expensive structural changes.
3. Architectural Flexibility and Cost-Efficiency
The architectural flexibility of PNK buildings is another standout feature. Our reinforced concrete frames offer the same cost efficiency as traditional construction methods but with the added benefit of much greater adaptability. Our buildings allow for easy upgrades and modifications in the future, ensuring that any changes required by the client or investor—whether in terms of layout, design, or function—can be accommodated with minimal additional investment.
What does this mean for you? It means that when you build with PNK, you’re not just getting a static structure—you’re investing in a future-proof asset that can evolve to meet the changing needs of your business.
4. Factory-Controlled Construction
Our manufacturing process is one of the key differentiators that set us apart from other construction firms. By producing standardized structural elements—including foundation components—in our own facilities, we can maintain high levels of control over quality and timing. Our production facilities, located in Pennsylvania and Georgia, are fully equipped to handle construction elements in any weather conditions, meaning we can proceed with construction without delay, regardless of external factors.
This factory-controlled approach also ensures a level of precision that minimizes the risk of defects and errors, which ultimately leads to fewer revisions and faster project completion.
Why Choose PNK Group?
When you work with PNK Group, you’re not just purchasing a building—you’re investing in a high-performance facility with a wide range of functional advantages that set it apart from others in its price category.
At PNK Group, we believe that industrial construction doesn’t have to be slow, inflexible, or costly. Our innovative approach to design, manufacturing, and construction ensures that you get a building that meets your current needs and can evolve with your business as it grows.
Ready to learn more about how PNK Group can accelerate your next industrial project?
Contact us today to discuss your needs and discover how our fast, flexible, and cost-effective solutions can transform your industrial space.
PNK Group continues its expansion in the Tri-State Area
March 20 – PNK Group continues its expansion in the Tri-State Area
Next-generation industrial building developer PNK Group has purchased a site in Connecticut.
Industrial developer PNK GROUP completed the acquisition of a 21.75-acre site in Windsor, CT near Hartford in February 2025. The company plans to construct a 218,000-square-foot industrial building on this site.
The Windsor site is less than five miles from I-91 (Exit 40) and is also in close proximity to Bradley International Airport. The convenient location makes the site perfect for both manufacturing and distribution centers, providing quick access to Massachusetts and the entire Tri-State Area (New York, New Jersey, Connecticut).
The local industry cluster already includes Amazon, Dollar Tree, Ford, Honda, FedEx, Walgreens, Eversource and many others among its corporate users. In addition, the Hartford metropolitan area is home to more than 1.2 million people, making it much easier to find and hire staff.
The acquisition of the Windsor site is part of PNK Group’s strategy to establish a foothold on the East Coast of the United States. Over the past half year, the company has increased its presence in PA, VA, CT, NJ by acquiring nearly 400 acres of land on which it will build several million square feet of industrial buildings.
PNK Group buildings are highly versatile and can be customized for various purposes – from production to distribution. The company uses technology that significantly speeds up the entire construction process compared to traditional methods. With standardized large-unit blocks produced at PNK’s own factories in Georgia and Pennsylvania, the company constructs buildings efficiently and faster than the average market construction time.
As an engineering and manufacturing pioneer, PNK Group spearheads technological advancements in industrial construction. The company’s construction methodology, utilizing large-unit blocks, streamlines building assembly through precise element production, minimizing the need for extensive labor and heavy machinery.
PNK Group has finished a new building near Atlanta
March 12 – PNK Group has finished a new building near Atlanta
Next-generation industrial building developer PNK Group has constructed a 1.2 million-square-foot facility.
PNK Group has completed a new industrial building in the town of McDonough, 35 miles from downtown Atlanta. The 1,219,826-square-foot PNK Lambert A building is complete and can accommodate future owners at any time. It can be used for manufacturing, warehousing or as a distribution center. The design includes the option to expand the space to 1.532 million square feet or provide additional parking.
PNK Lambert A is part of the PNK Park Southern Gateway industrial park, which in turn is part of a larger cluster that is home to such corporations as Ecolab, Horizon Group USA, Whirpool, The Home Depot, Kimberly-Clark, and many others. This location is important to companies that distribute goods in the Atlanta metropolitan area, as well as manufacturing companies.
The industrial park is located just two miles from I-75 highway connecting the Southeast to the Midwest. It offers convenient access to the major seaports of Savannah in Georgia, Charleston in South Carolina and Jacksonville in Florida.
The design features of the new multifunctional building allow the installation of an overhead crane with a lifting capacity of up to eight tons at any desired location. The structural stability of the building is enhanced with Self-stable prefab precast concrete columns and footer one solid unit with a rebar reinforced frame. Column spacing is 50 feet by 56 feet. The depth of the speed way is 60 feet.
PNK Lambert A features reinforced concrete floors (8” slab thickness, 4000 psi, reinforced with steel prefab mesh) to withstand heavy equipment and high loads. The building’s roof has a 60 mil, R-25 TPO membrane and Internal Siphonic Roof Drain System. System eliminates contamination and icing of the Truck Court. The facility has state-of-the-art utility systems. Lighting – 30 FC on 15’ Whips (and motion sensors). Ventilation – MAU/ 3 air changes (louvers and mechanical damper, freeze protection).
The building was constructed using PNK technology. For this purpose, high-precision reinforced precast concrete structural frame and other standardized elements were produced in advance at the company’s own plants in Pennsylvania and Georgia, which allowed to level out the human factor, and the work was completed much faster than the market average.
As an engineering and manufacturing pioneer, PNK Group spearheads technological advancements in industrial construction. The company’s construction methodology, utilizing large-unit blocks, streamlines building assembly through precise element production, minimizing the need for extensive labor and heavy machinery.

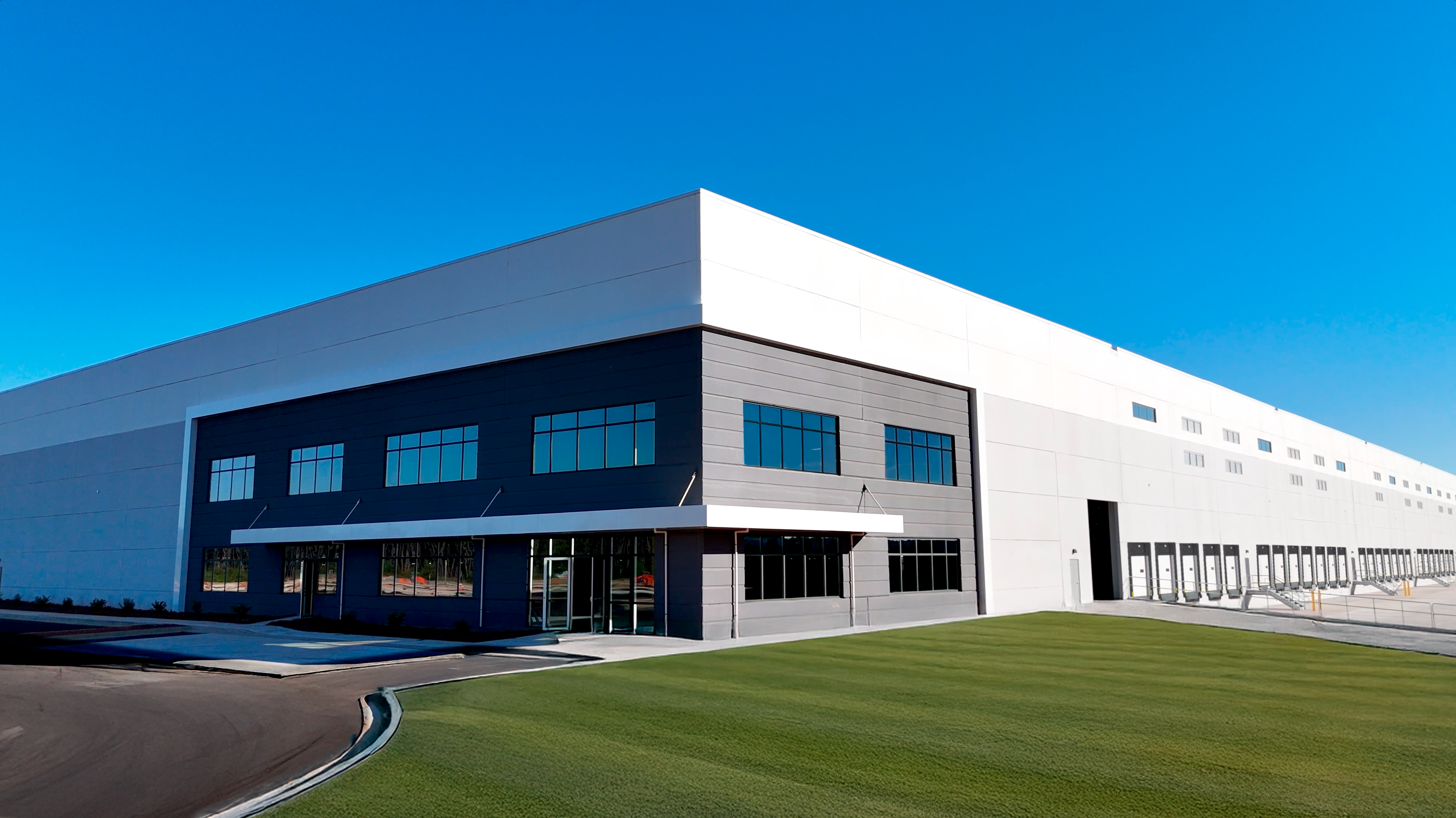
PNK Group has invested $120 million in a building for Ecolab in North Carolina.
January 28 — PNK Group has invested $120 million in a building for Ecolab in North Carolina.
PNK Group, developer of a new generation of industrial buildings, has built a
distribution center with more than 1 million square feet of space.
The new industrial building located in High Point, North Carolina became the
second building constructed by PNK Group for Ecolab Corporation, a major global leader in water, hygiene and infection prevention solutions.
PNK Group’s investment in this building was approximately $120 million. PNK
Group bought the land, designed the building and supervised the entire
construction process. The total area of the building, that has been already handed
over to the Customer, is 1,057,564 square feet.
The first distribution center was built in Atlanta and became part of the PNK
Southern Gateway Industrial Park. The new cooperation confirmed that the
partners trust each other and the customer is satisfied with the level and quality
of the building.
As an engineering and manufacturing pioneer, PNK Group spearheads
technological advancements in industrial construction. The company’s
construction methodology, utilizing large-unit blocks, streamlines building
assembly through precise element production, minimizing the need for extensive
labor and heavy machinery.
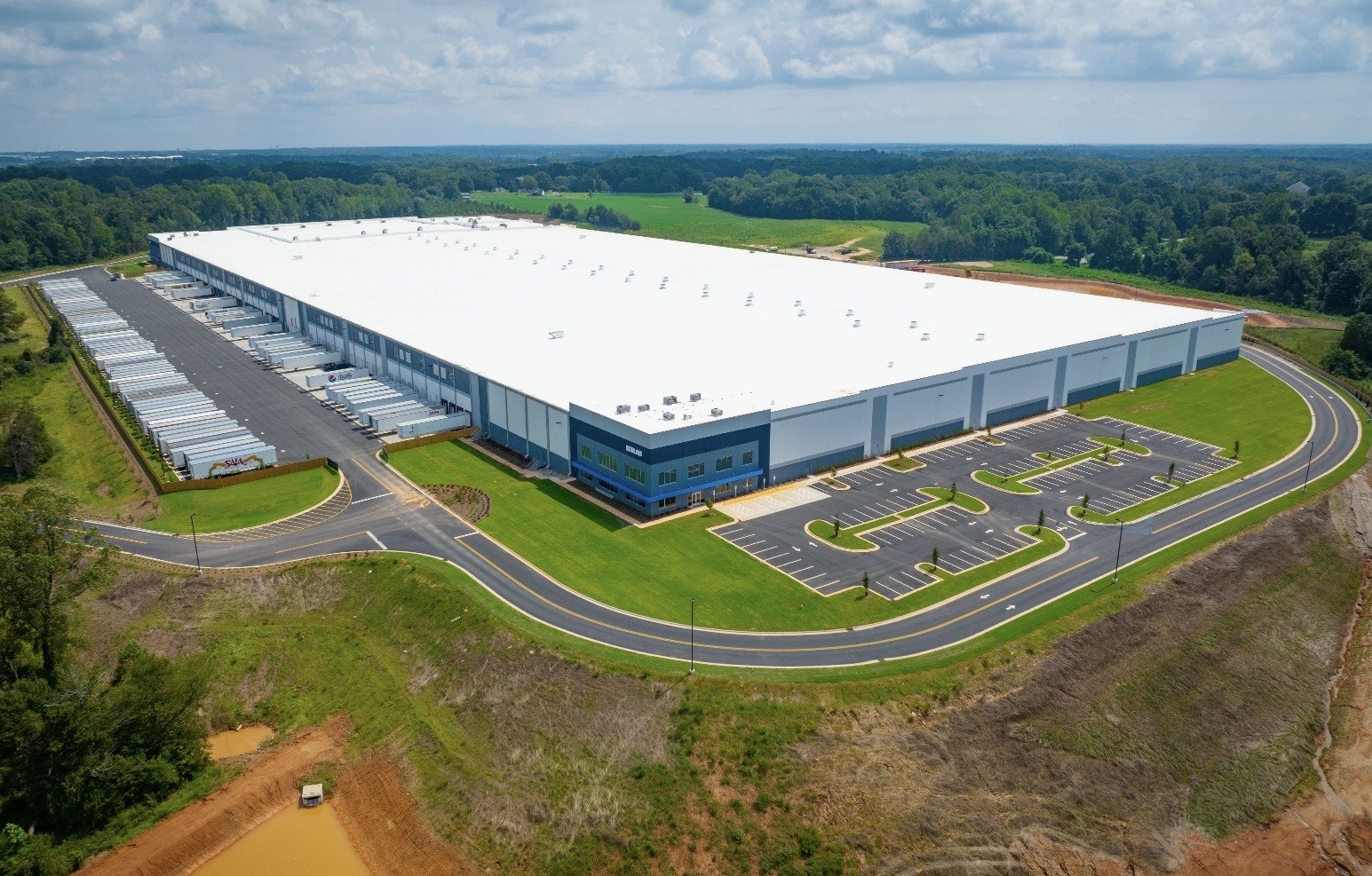
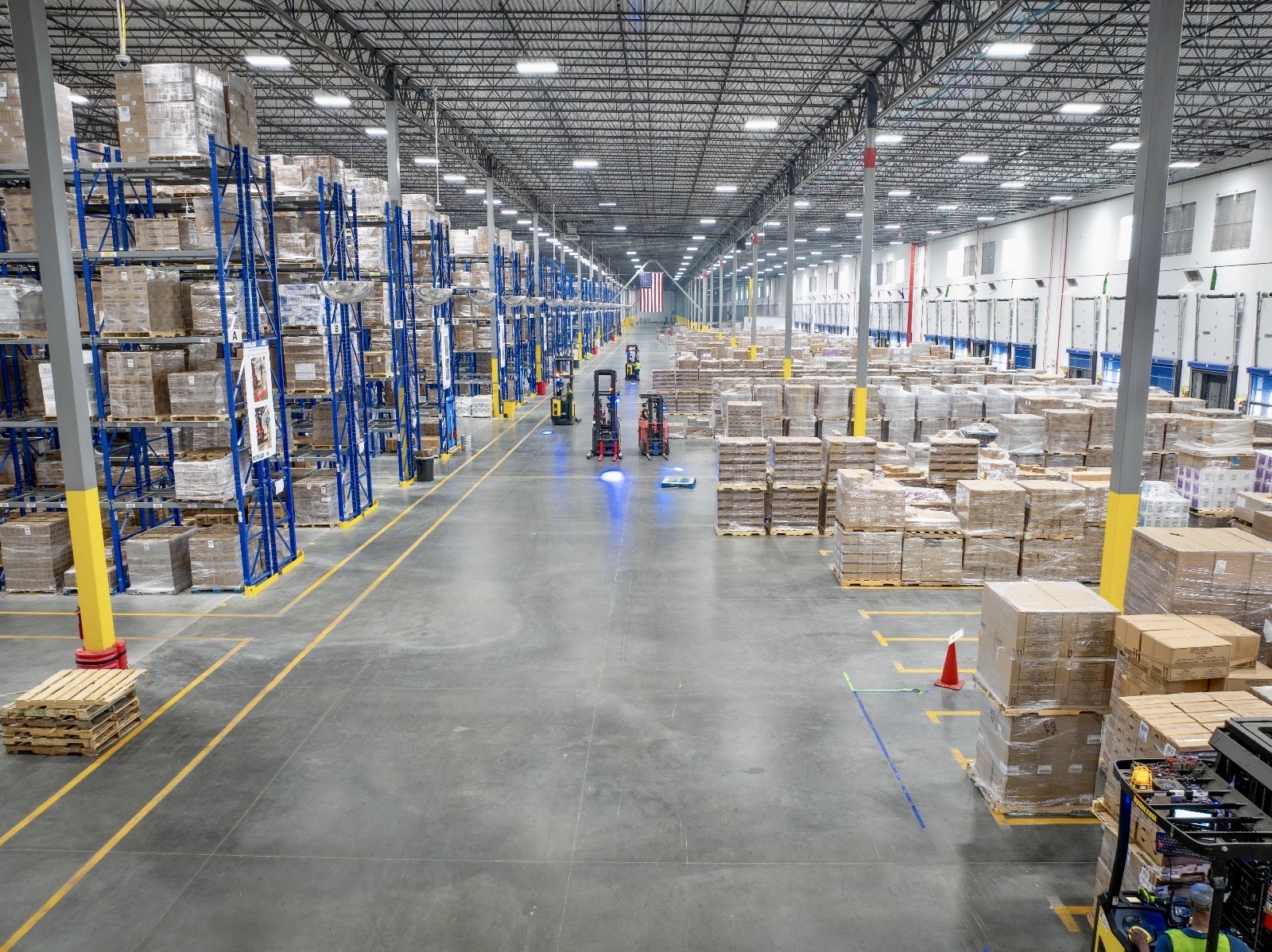